Advantages
Quality Assurance System
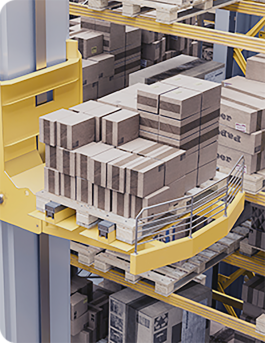
Supplier Grading System
Level 1: Original Manufacturers, Distributors, Catalog Distributors
Level 2: OEM/ODM/EMS Factories
Level 3: Non-compliant Suppliers
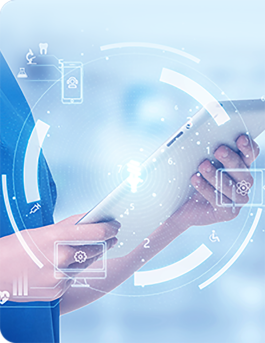
Quality Control &
Data Management
Material System Inbound and Outbound Records
Detailed Photos of Material Inbound
Detailed Photos of Material Outbound
Quality Assurance Letter
Timely Update of Database System
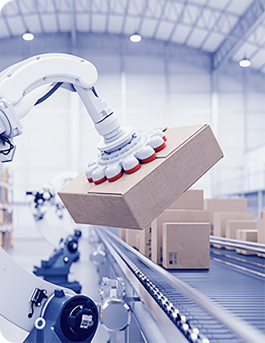
Storage, Packaging &
Transportation Standards
Implement ESD (Electrostatic Discharge) Protection Control
Custom Packaging and Labeling
Establish records for each customer's shipping requirements and choose the fastest, safest, and most economical transportation methods
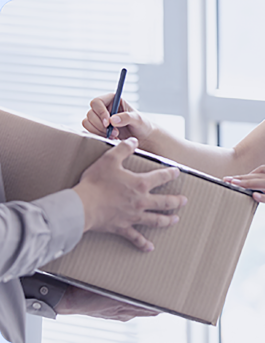
PMA Return Process
Commit to responding to customer RMA requests within 6 hours and actively provide solutions.
If a material quality issue is confirmed, commit to a full recall of the material and cover all transportation costs.
Quality Assurance Process
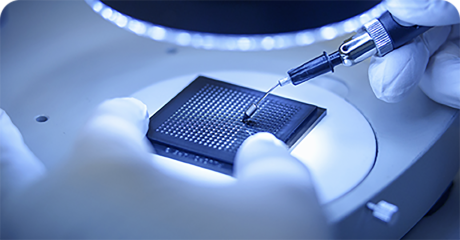
Visual Inspection

Brand, Model, Quantity, Production Date, and ROHS Compliance Inspection
Outer Packaging Inspection, checking if the packaging is intact/completed and if the packaging materials meet the relevant MSL (Moisture Sensitivity Level) standards
Silkscreen Marking Inspection, Consistency Check, and Verification Against Original Manufacturer Specifications
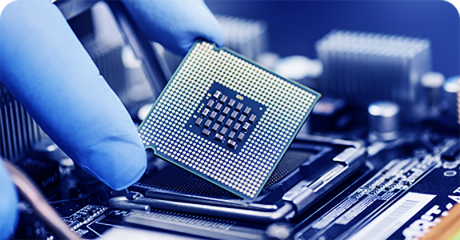
Quality Test

Solderability Test
X-Ray Consistency Test
XRF/EDX/EDS Testing" (X-Ray Fluorescence, Energy-Dispersive X-ray Spectroscopy)
Functionality Test
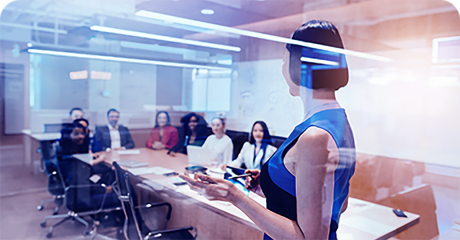
Training System

All employees are required to participate in training courses, not limited to the quality management team.
The Yicheng training program helps us understand the latest trends in the manufacturing industry, best practices, and new counterfeiting techniques.
Quality manager has an average of 8 years of experience in their field.